Capture geometry with OpenSCAN
- Adaptive Technology
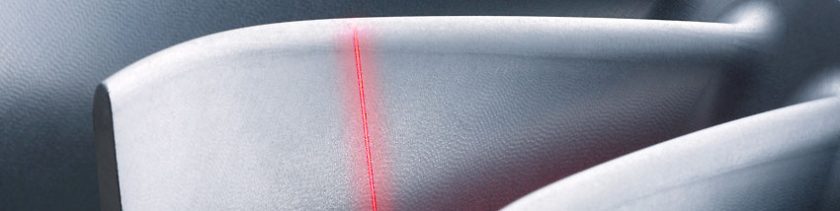
OpenSCAN
To be able to take account of individually shaped parts or special clamping situations within the scope of adaptive machining, we first have to determine the differences between the actual situation and the nominal situation (CAD). All adaptive systems either come with integrated measurement devices – or are connected to such devices – for this purpose.
In the simplest case, the differences can be determined with touch trigger probes. In most cases, these have already been incorporated in the NC machines by the machinery manufacturer and permit reliable measurement of individual points. The BCT solutions for adaptive machining include integrated measurement modules with which measurement sequences can be defined and results displayed.
However, if the machining task requires a large number of measurement points, laser line scanning is more suitable. With this method the distances between the sensor and a strip projected onto the part are evaluated point by point. This method is very fast and simultaneously delivers a large number of measurements points. These measurement procedures can be defined with OpenSCAN. The precision of the measurements is increased by special compensations – in particular, when these are undertaken from different directions (OpenSCAN is available for the Sinumerik 840D).
Your Advantages:
- Measurement of the part in the machine
- Short measurement times together with a high resolution
- Capturing part states for various purposes
Applications
Capturing the geometry of carbon-fiber parts
During the scarfing of workpieces made of composite material, individual layers have to be removed in a defined way. Knowledge of the part’s geometry is a basic prerequisite in this context. Area data can be captured quickly and precisely via laser line scanning.
Reprofiling of leading and trailing edges of fan blades
The actual shapes of the leading and trailing edges are captured in a first process step. Laser line scanning delivers the corresponding data with high accuracy. With the aid of actual data, the software then calculates the NC programs for reconstructing the desired profile.
3D printing
A scan made with a laser line sensor serves to monitor the interim results after the deposition of a certain number of layers during laser fusion welding. The captured state can be used to adapt the subsequent process steps.